3D CAD MATRIX COURSE IN JAIPUR

FREE DEMO CLASSES
What is 3D CAD?
3D CAD, or three-dimensional computer-aided design, is a technology used by engineers, architects, designers, and manufacturers to create, modify, analyze, and optimize three-dimensional models of products or structures. It’s an integral part of modern design and engineering workflows, offering significant advantages over traditional 2D drafting methods.
“Matrix” is a term that holds various meanings across different fields, from mathematics and computer science to biology and philosophy. At its core, a matrix is a structured arrangement of elements in rows and columns, forming a rectangular array. This arrangement serves as a fundamental concept with wide-ranging applications, making it a cornerstone of numerous disciplines.
In mathematics, a matrix provides a concise and systematic way to represent and manipulate data, equations, and transformations. It serves as a powerful tool in linear algebra, where matrices are used to solve systems of linear equations, perform vector transformations, and analyze geometric properties.
In computer science, matrices play a vital role in fields such as graphics, machine learning, and cryptography. They are used to represent images, perform operations in neural networks, and encrypt data for secure communication.
Biologists utilize matrices to organize and analyze biological data, such as genetic sequences, protein interactions, and ecological relationships. Matrices help researchers identify patterns, infer evolutionary relationships, and model complex biological systems.
Moreover, the concept of a matrix extends beyond the realms of mathematics and science into philosophy, where it symbolizes interconnectedness, patterns, and systems of thought. Philosophical frameworks such as the “matrix of consciousness” or the “matrix of reality” explore the interconnected nature of existence and perception.
In essence, the concept of a matrix transcends disciplinary boundaries, serving as a versatile and foundational tool for understanding, organizing, and interpreting complex information and systems. Its significance spans from mathematical equations and computer algorithms to biological processes and philosophical inquiries, making it an essential concept in the pursuit of knowledge and understanding.
Understanding the basics of curves, surfaces, and solids is fundamental in various fields, including mathematics, computer graphics, engineering, and design. Let’s explore each of these concepts:
**Curves:**
Curves are continuous, smooth, and often geometrically defined paths in two-dimensional or three-dimensional space. They can be described mathematically using equations or parametric representations. Curves play a crucial role in various applications, including:
1. **Mathematics**: Curves are studied extensively in mathematics, particularly in the branch of geometry. Examples include lines, circles, ellipses, parabolas, and hyperbolas.
2. **Computer Graphics**: In computer graphics, curves are used to create smooth shapes and contours in 2D and 3D models. Popular curve types include Bézier curves, spline curves, and NURBS (Non-Uniform Rational B-Splines).
3. **Engineering and Design**: Engineers and designers use curves to define the shape of objects, such as aircraft wings, car bodies, and architectural forms. Curves help create aesthetically pleasing and functional designs.
**Surfaces:**
Surfaces are two-dimensional geometric entities that define the boundary or exterior of a three-dimensional object. Like curves, surfaces can be described using mathematical equations or parametric representations. Surfaces are vital in various fields, including:
1. **Mathematics**: Surfaces are extensively studied in differential geometry, where they are classified based on their intrinsic properties, such as curvature and topology.
2. **Computer-Aided Design (CAD)**: Surfaces are used in CAD software to model complex 3D shapes and objects. Designers can create surfaces by lofting, sweeping, or extruding curves, or by directly manipulating surface control points.
3. **Manufacturing and Engineering**: Surfaces play a crucial role in manufacturing processes such as machining, molding, and casting. Engineers use surface representations to ensure that manufactured parts meet specified tolerances and surface finish requirements.
**Solids:**
Solids are three-dimensional objects that occupy space and have volume. They are defined by their surfaces and interior boundaries. Solids come in various shapes and forms, including prisms, pyramids, cylinders, cones, and spheres. Understanding solids is essential in:
1. **Geometry**: Solid geometry deals with the study of three-dimensional shapes, their properties, and relationships. It includes topics such as volume, surface area, and spatial relationships between solids.
2. **Engineering and Architecture**: Engineers and architects use solid models to design and analyze structures, buildings, and mechanical components. Solid modeling software allows designers to create, modify, and simulate solid objects with precision.
3. **Manufacturing and Prototyping**: Solids are crucial in manufacturing processes such as 3D printing, CNC machining, and injection molding. Solid models are used to generate toolpaths, molds, and prototypes for production.
In summary, curves, surfaces, and solids are fundamental concepts that play a vital role in mathematics, engineering, design, and manufacturing. Understanding these concepts enables professionals to create, analyze, and manipulate geometric shapes and structures with precision and efficiency.
Parametric modeling and design is a powerful approach used in various fields such as engineering, architecture, product design, and computer graphics. It involves creating digital models of objects or systems using parameters that define their geometric and functional characteristics. Here’s an overview of parametric modeling and design:
**1. Parameters:**
Parameters are variables or values that define specific aspects of a model. These parameters can include dimensions, angles, distances, materials, and other properties. By adjusting these parameters, designers can modify the shape, size, and behavior of the model, allowing for easy exploration of design alternatives.
**2. Relationships:**
In parametric modeling, objects are defined not only by their geometry but also by relationships between parameters. These relationships can be simple (e.g., a rectangular shape defined by its length and width) or complex (e.g., a dynamic linkage mechanism with multiple moving parts). Changes to one parameter can automatically propagate through the model, adjusting other parameters accordingly.
**3. Constraints:**
Constraints are rules or conditions that govern the behavior of parameters and relationships in a parametric model. They enforce design requirements, such as maintaining specific dimensions, maintaining symmetry, or ensuring that parts fit together properly. Constraints help ensure that the model remains valid and functional as parameters are modified.
**4. Parametric Modeling Software:**
Parametric modeling software, such as computer-aided design (CAD) tools, provides a platform for creating, editing, and analyzing parametric models. These software packages offer intuitive interfaces for defining parameters, relationships, and constraints, as well as tools for visualizing and simulating the model’s behavior.
**5. Benefits of Parametric Modeling:**
Parametric modeling offers several advantages over traditional modeling approaches:
– **Flexibility:** Parametric models are highly adaptable and can easily accommodate design changes and iterations.
– **Efficiency:** By defining relationships and constraints, parametric modeling streamlines the design process and reduces the time required to explore design alternatives.
– **Accuracy:** Parametric models maintain geometric and functional integrity, ensuring that changes to one part of the model are accurately reflected throughout the design.
– **Automation:** Parametric modeling software can automate repetitive tasks, such as generating drawings, bills of materials, and simulations, increasing productivity and reducing errors.
**6. Applications:**
Parametric modeling and design are widely used in various industries and applications, including:
– Engineering: Designing mechanical components, structures, and systems.
– Architecture: Creating buildings, interiors, and urban environments.
– Product Design: Developing consumer products, appliances, and machinery.
– Animation and Visual Effects: Modeling characters, props, and environments for film and video games.
In summary, parametric modeling and design revolutionize the way objects and systems are conceived, created, and analyzed, offering designers and engineers unprecedented flexibility, efficiency, and control over the design process.
Building and cutting diamonds is a highly specialized craft that requires precision, skill, and attention to detail. Let’s delve into the intricate process of diamond building and cutting:
**1. Diamond Building:**
Diamond building, also known as diamond synthesis or diamond manufacturing, is the process of creating diamonds in a laboratory setting. While natural diamonds form deep within the Earth over millions of years, diamond building utilizes high-pressure, high-temperature (HPHT) or chemical vapor deposition (CVD) methods to grow diamonds under controlled conditions.
**High-Pressure, High-Temperature (HPHT) Method:**
– In the HPHT method, a small diamond seed crystal is placed in a pressurized chamber along with carbon source material (typically graphite) and a catalyst metal.
– The chamber is subjected to extreme pressure (around 5-6 GPa) and high temperature (over 1,500°C), replicating the conditions found deep within the Earth’s mantle where natural diamonds form.
– Over time, carbon atoms from the source material adhere to the diamond seed crystal, gradually building up layers of diamond structure.
– The process can take several days to weeks to produce a usable diamond, depending on the desired size and quality.
**Chemical Vapor Deposition (CVD) Method:**
– In the CVD method, a diamond seed substrate (such as a thin slice of natural diamond or synthetic diamond) is placed in a vacuum chamber.
– A mixture of gases containing carbon (such as methane) is introduced into the chamber, along with a source of energy (such as microwaves or lasers).
– The energy breaks down the gas molecules, allowing carbon atoms to deposit onto the seed substrate and form a diamond layer.
– The diamond grows atom by atom, layer by layer, resulting in a high-quality synthetic diamond.
– CVD diamonds can be produced with specific characteristics, such as color and purity, making them ideal for various industrial and technological applications.
**2. Diamond Cutting:**
Diamond cutting is the art of shaping and faceting rough diamonds into polished gems of exquisite beauty and brilliance. Skilled diamond cutters use precision tools and techniques to unlock the full potential of each rough diamond, maximizing its fire, sparkle, and optical properties.
**Key Steps in Diamond Cutting:**
– **Planning:** Before cutting begins, the rough diamond is carefully examined to determine the optimal shape and proportions that will maximize its beauty and value.
– **Cleaving or Sawing:** In this initial step, the rough diamond may be cleaved (split) along its natural cleavage planes using a sharp blade or saw to separate it into smaller, more manageable pieces.
– **Bruting:** Next, the diamond is shaped into a preliminary form known as a “bruted” or “girdled” stone, typically with a round or oval outline. This is achieved by grinding the edges of the diamond against each other to create the desired shape.
– **Faceting:** The most intricate and precise step, faceting involves cutting and polishing a series of flat, geometric surfaces (facets) onto the diamond’s surface. These facets are strategically positioned to optimize the diamond’s brilliance, dispersion, and scintillation.
– **Final Polishing:** Once all facets have been cut, the diamond undergoes a final polishing process to remove any remaining surface imperfections and enhance its luster and clarity.
**Conclusion:**
Diamond building and cutting represent the convergence of science, technology, and artistry, resulting in the creation of some of the most coveted and enduring symbols of beauty and luxury. Whether produced through advanced laboratory techniques or meticulously crafted by skilled artisans, diamonds continue to captivate and inspire with their timeless elegance and allure.
Certainly! Stones come in a variety of shapes, each with its own unique characteristics and aesthetic appeal. Here are some of the different types of stone shapes commonly used in jewelry and decorative applications:
**1. Round:**
– Round stones are perhaps the most classic and popular shape, characterized by a circular outline.
– They are known for their timeless elegance and exceptional brilliance, as their symmetrical shape maximizes light reflection.
**2. Princess:**
– Princess-cut stones feature a square or rectangular shape with sharp, pointed corners.
– They are prized for their modern and sophisticated appearance, offering a blend of brilliance and geometric precision.
**3. Emerald:**
– Emerald-cut stones have a rectangular or square shape with trimmed corners and a step-cut faceting style.
– They are renowned for their understated elegance and elongated silhouette, which emphasizes clarity and color.
**4. Oval:**
– Oval stones are elongated with a rounded outline, similar to the shape of an egg.
– They are favored for their flattering appearance on the finger and their ability to create the illusion of longer, slender fingers.
**5. Marquise:**
– Marquise-cut stones feature a distinctive elongated shape with pointed ends, resembling a boat or a football.
– They are prized for their unique silhouette and their ability to create the illusion of greater size due to their elongated proportions.
**6. Pear:**
– Pear-shaped stones, also known as teardrop or drop-cut stones, combine the rounded end of a round stone with the pointed end of a marquise.
– They are cherished for their graceful and romantic appearance, making them a popular choice for engagement rings and pendants.
**7. Cushion:**
– Cushion-cut stones have a square or rectangular shape with rounded corners, resembling a pillow or cushion.
– They are celebrated for their vintage charm and their ability to showcase a stone’s color and clarity with their large facets and gentle curves.
**8. Heart:**
– Heart-shaped stones feature a silhouette that resembles the outline of a heart, symbolizing love and romance.
– They are often chosen for sentimental jewelry pieces such as engagement rings and pendants, making them a heartfelt expression of affection.
**9. Asscher:**
– Asscher-cut stones are similar to emerald-cut stones but with a square shape and more step-like facets.
– They are admired for their Art Deco-inspired elegance and their ability to exude vintage glamour and sophistication.
**10. Radiant:**
– Radiant-cut stones combine the brilliance of round stones with the sleek lines of emerald and princess cuts.
– They feature a square or rectangular shape with trimmed corners and a brilliant-cut faceting style, offering a dazzling display of sparkle and fire.
These are just a few examples of the diverse range of stone shapes available, each with its own allure and charm. Whether classic and timeless or modern and avant-garde, the choice of stone shape can greatly influence the overall style and personality of a piece of jewelry or decorative item.
Creating a realistic visualization and rendering involves using advanced computer graphics techniques to generate images that closely resemble real-world scenes or objects. Whether for architectural visualization, product design, or animation, achieving realism requires attention to detail, understanding of lighting and materials, and proficiency with rendering software. Here’s a step-by-step guide to creating realistic visualizations and renderings:
**1. Model Creation:**
Begin by creating or importing 3D models of the objects or scenes you want to visualize. This could include architectural models, product designs, or characters for animation. Use modeling software such as Autodesk Maya, Blender, or SketchUp to build detailed and accurate geometry.
**2. Texturing and Materials:**
Apply realistic textures and materials to your 3D models to simulate the appearance of real-world surfaces. This involves assigning materials such as wood, metal, glass, or fabric to different parts of your model and adjusting parameters like color, roughness, and reflectivity. Use texture maps for additional detail, such as bump maps for surface imperfections or displacement maps for fine geometry details.
**3. Lighting Setup:**
Lighting plays a crucial role in creating realistic visualizations. Experiment with different lighting setups to achieve the desired mood and atmosphere. Use techniques such as global illumination, image-based lighting, and HDR lighting to simulate natural light behavior. Position lights strategically to highlight important features and create shadows that add depth and realism to your scene.
**4. Camera Placement and Composition:**
Consider the camera angle, framing, and composition of your scene to create visually appealing images. Experiment with different camera angles and perspectives to find the most effective way to showcase your design. Use techniques such as depth of field, focal length, and camera movement to draw the viewer’s attention to key elements of your scene.
**5. Rendering Settings:**
Configure the rendering settings of your software to achieve high-quality results. Adjust parameters such as resolution, anti-aliasing, ray tracing quality, and render samples to balance rendering speed with image quality. Consider using a physically-based rendering (PBR) workflow for accurate light interaction and material rendering.
**6. Post-Processing:**
After rendering, fine-tune your images using post-processing techniques to enhance realism and aesthetics. This may include color correction, contrast adjustments, adding lens effects such as bloom or glare, and compositing multiple passes for greater control over the final look.
**7. Feedback and Iteration:**
Gather feedback from colleagues, clients, or peers and iterate on your visualizations based on their input. Pay attention to details such as material accuracy, lighting realism, and overall composition to continuously improve the quality of your renderings.
By following these steps and incorporating best practices in modeling, texturing, lighting, and rendering, you can create stunning and realistic visualizations that effectively communicate your design intent and captivate viewers.
In a matrix software, the development settings typically refer to the configuration and customization options available to users for tailoring the software to their specific needs and workflows. Here’s an outline of what the development settings might encompass in a matrix software:
**1. User Interface Customization:**
Users can customize the layout, appearance, and behavior of the software’s user interface to optimize their workflow. This may include rearranging toolbars, docking panels, and adjusting color schemes or font sizes for improved readability.
**2. Scripting and Automation:**
Advanced users may have access to scripting tools or programming interfaces for automating repetitive tasks, creating custom tools, or extending the functionality of the software. This could involve scripting languages like Python, JavaScript, or proprietary scripting languages specific to the software.
**3. Plug-in Support:**
The software may support plug-ins or extensions developed by third-party developers, allowing users to enhance the software’s capabilities with additional features or specialized tools. Users can install, manage, and configure plug-ins according to their requirements.
**4. Data Management and Integration:**
Development settings may include options for managing and integrating data from external sources, such as databases, spreadsheets, or other software systems. Users can define data connections, import/export data, or establish interoperability with other software platforms.
**5. API (Application Programming Interface) Access:**
The software may expose an API that allows developers to interact programmatically with its functionalities. This enables the creation of custom integrations, automation scripts, or external applications that interact with the software.
**6. Customization of Algorithms and Algorithms Settings:**
In a matrix software used for mathematical or computational purposes, users may have the ability to customize algorithms or algorithm settings to fine-tune performance or adapt to specific use cases. This could involve adjusting parameters, selecting optimization strategies, or implementing custom algorithms.
**7. Version Control and Collaboration:**
For collaborative development environments, the software may offer version control features, allowing users to track changes, manage revisions, and collaborate with team members on shared projects. This could include integration with version control systems like Git or Subversion.
**8. Documentation and Support:**
Comprehensive documentation and support resources are essential for users to leverage the development settings effectively. This may include tutorials, guides, reference documentation, and community forums where users can exchange knowledge and seek assistance.
By providing robust development settings, a matrix software empowers users to tailor the software to their specific requirements, automate tasks, extend functionality, and integrate seamlessly with other tools and systems, ultimately enhancing productivity and enabling innovative solutions.
Developing industry-specific applications involves creating software solutions tailored to the unique needs, workflows, and challenges of particular industries. Here’s a step-by-step guide to developing industry-specific applications:
**1. Identify Industry Needs:**
Understand the specific requirements, pain points, and opportunities within the target industry. Conduct thorough research, gather feedback from stakeholders, and identify key functionalities and features that address industry-specific challenges.
**2. Define Use Cases:**
Define use cases and scenarios that illustrate how the application will be used in real-world situations within the target industry. Identify common tasks, processes, and workflows that the application should support, and prioritize features based on their importance and impact.
**3. Design User Experience (UX):**
Design a user experience (UX) that is intuitive, efficient, and tailored to the needs of industry professionals. Consider factors such as ease of use, task efficiency, accessibility, and compatibility with existing tools and systems used in the industry.
**4. Develop Functionalities:**
Develop the core functionalities of the application based on the identified use cases and requirements. This may involve implementing features such as data management, workflow automation, reporting and analytics, collaboration tools, and integration with third-party systems.
**5. Implement Industry-Specific Logic:**
Incorporate industry-specific logic, rules, and algorithms into the application to address the unique requirements of the target industry. This may include custom algorithms, calculations, validations, or business rules that reflect industry standards and best practices.
**6. Ensure Compliance and Security:**
Ensure that the application complies with industry regulations, standards, and security requirements. Implement measures to protect sensitive data, ensure data privacy, and prevent unauthorized access or breaches.
**7. Test and Quality Assurance (QA):**
Thoroughly test the application to identify and address any bugs, errors, or issues. Conduct functional testing, usability testing, performance testing, and compatibility testing to ensure that the application meets industry standards and user expectations.
**8. Provide Training and Support:**
Provide comprehensive training and support to industry professionals who will be using the application. Offer user documentation, training materials, tutorials, and customer support resources to help users maximize the value of the application and address any questions or concerns.
**9. Iterate and Improve:**
Continuously gather feedback from users and stakeholders, monitor usage metrics and performance indicators, and iterate on the application to incorporate enhancements, updates, and new features. Maintain a feedback loop to ensure that the application evolves to meet the changing needs of the industry.
By following these steps and leveraging industry-specific knowledge and expertise, developers can create tailored applications that address the unique requirements and challenges of particular industries, ultimately providing value and driving innovation within those sectors.
Why Choose 3D CAD?
-
3D CAD, or three-dimensional computer-aided design, is a technology used by engineers, architects, designers, and manufacturers to create, modify, analyze, and optimize three-dimensional models of products or structures. It’s an integral part of modern design and engineering workflows, offering significant advantages over traditional 2D drafting methods.
Here are some key aspects of 3D CAD:
1. **Three-Dimensional Modeling**: Unlike traditional 2D CAD, which represents designs using flat, two-dimensional drawings, 3D CAD enables the creation of digital models that accurately depict the geometry and spatial relationships of objects in three dimensions. This allows designers to visualize, manipulate, and analyze their designs more effectively.
2. **Parametric Design**: One of the fundamental features of 3D CAD is parametric modeling, where the dimensions, features, and relationships of objects are defined by parameters. This enables designers to make changes to the design at any stage of the process, with the software automatically updating the model and associated drawings accordingly.
3. **Assembly Design**: 3D CAD software allows designers to create complex assemblies consisting of multiple components. These assemblies can be assembled, disassembled, and analyzed virtually, allowing designers to ensure proper fit, function, and interferences before physical prototyping or manufacturing.
4. **Visualization and Rendering**: 3D CAD software typically includes tools for rendering and visualizing designs in realistic detail. This allows designers to create high-quality renderings and presentations for communicating their ideas to clients, stakeholders, or manufacturing teams.
5. **Simulation and Analysis**: Many 3D CAD programs offer simulation and analysis tools for evaluating the performance, strength, and behavior of designs under various conditions. This includes finite element analysis (FEA) for structural analysis, computational fluid dynamics (CFD) for fluid flow simulation, and other specialized tools for thermal analysis, motion simulation, and more.
6. **Collaboration and Documentation**: 3D CAD software facilitates collaboration among team members by providing tools for sharing, reviewing, and annotating designs. It also generates detailed documentation, including drawings, bills of materials (BOMs), and manufacturing instructions, to support the manufacturing and assembly processes.
Overall, 3D CAD is a powerful tool that revolutionizes the design and engineering process, enabling faster iteration, better visualization, and more accurate analysis, ultimately leading to improved product quality and reduced time to market.
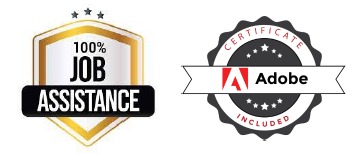

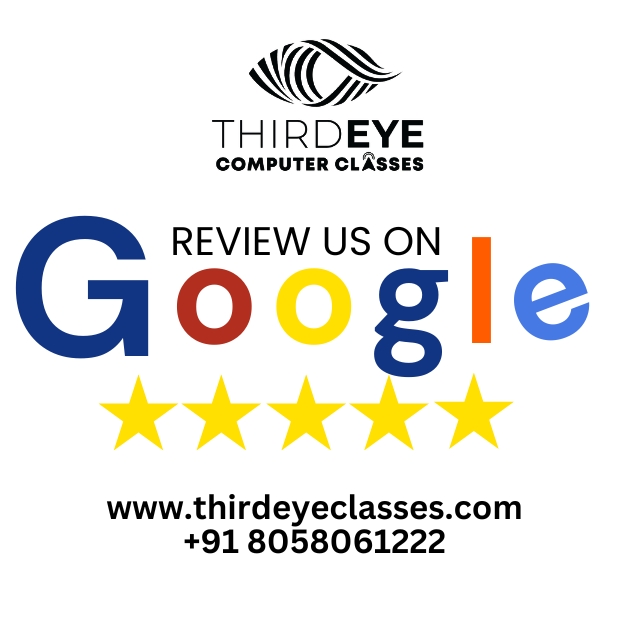
Placements of Thirdeye
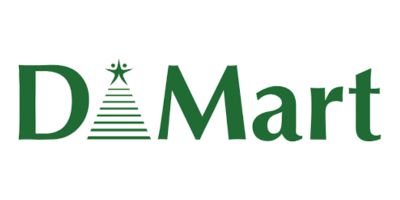
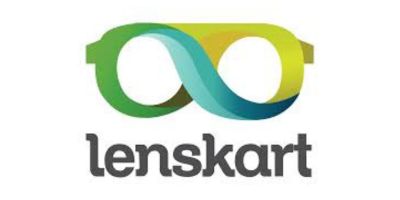

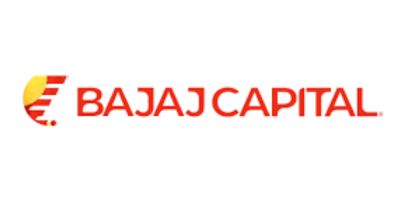

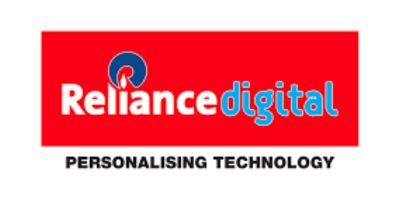
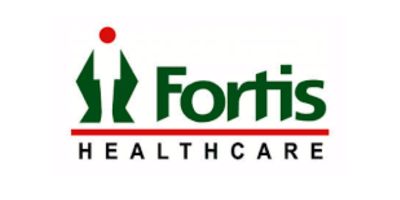